Tool nose radius compensation chart download
- Fanuc gt; tool nose compensation problem.
- Tool Nose Radius Comp Calculator only G1 - CNC.
- Tool Nose Radius Compensation - CNC Training Centre.
- CNC Training, Rose Training, Swiss-Turning, Fundamental CNC, Tooling.
- Tool Path Generation for Multi-Degree-of-Freedom Fast Tool Servo.
- Schematic illustration of tool nose radius compensation | Download.
- Lathe Tool Nose Radius Compensation - MachMotion.
- Surface Finish Cross Reference Chart - Octane Workholding LLC.
- Tool Nose Radius Offset | AS PRECISION.
- Introduction to Turning Tools and Their Application.
- Nose Radius - an overview | ScienceDirect Topics.
- Solved: Compensation - Autodesk Community.
- How to Calculate CNC Lathe Tool Nose Radius Compensation the... - YouTube.
Fanuc gt; tool nose compensation problem.
Oct 23, 2019 Ro.8. BRIEF REVIEW. Tool nose radius offset is nothing more for a lathe than a cutter radius offset for a mill. It#39;s just a different name for the same control feature. Some CNC lathe manufacturers prefer to separate these terms, to suggest that there are some differences between radius offset in milling and turning. Apr 1, 1997 Just as cutter radius compensation allows the programmer to program work surface coordinates, so does tool nose radius compensation. Figure 5 stresses why tool nose radius compensation is required. As you can see, when work surface coordinates are programmed, the tool#39;s radius will cause deviations from the work surface on circular and angular. Tool nose radius compensation allows you to program the work surface path all coordinates right on the workpiece. It will automatically create the compensated path and keep the cutting edge flush with all workpiece surfaces. Second, some computer aided manufacturing CAM systems will create a CNC program with compensated tool paths.
Tool Nose Radius Comp Calculator only G1 - CNC.
To reduce vibration, it is often an advantage to choose a nose radius that is smaller than the depth of cut. 0 = Sharp corner .005R 1 = 1/64 radius 2 = 1/32 3 = 3/64 4 = 1/16 5 = 5/64 6 = 3/32 7 = 7/64 8 = 1/8 10 = 5/32 12 = 3/16 14 = 7/32 16 = 1/4 Large nose radius: Increased feed rates Large depths of cut Strong edge security. Jan 4, 2015 Re: new guy, need help understanding tool nose compensation. To answer your last question first: Treat the TL machines the same as you would a regular CNC lathe with the tool on the side opposite from the operator. Somewhere in the Toolroom Lathe addendum to the Lathe Manual this is mentioned. Actually if you look at the Graphics display on the. Dec 24, 2015 1. Add TNRC commands in the program. 2. Enter the nose radius of the tool at the machine 3. Enter the tool orientation at the machine This short explanation on TNRC tells you what it is, where it is used, and how its poor understanding causes agony on most shop floors.
Tool Nose Radius Compensation - CNC Training Centre.
By the way, tool nose radius compensation is used on lathes not mills and is not quite the same thing. The basic rules for cutter comp are 1. activate G41/G42 on a linear G01 move in a movement other than Z axis. This movement must be longer than the radius of the tool. 2. Specify the offset number in the same line as the comp call..
CNC Training, Rose Training, Swiss-Turning, Fundamental CNC, Tooling.
Carbide Insert Designation Chart. ANSI Code No. Inscribed Circle Size: ISO Code No. metric cutting edge length by shape code letter of insert. Tool nose radius goes hand in hand with this and must be considered when turning. See the provided tool nose radius pdf. where feed rate and depth of cut are equivalent. When referring to turned finishes, tool nose radius is one of the greatest determining factors in how fast you can feed and still achieve the same finish.
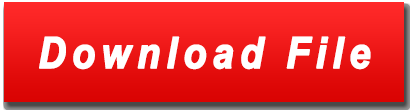
Tool Path Generation for Multi-Degree-of-Freedom Fast Tool Servo.
G41 or G42 will select tool nose compensation. G41 moves the tool to the left of the programmed path to compensate for the size of a tool and vice versa for G42. A tool offset must be selected with a Tnnxx code. where xx corresponds to the offsets that are to be used with the tool. 1.8.1 Roughing operations. In roughing turning operations, the nose radius should be selected as large as is permissible by the tool layout because: 1 it increases the strength of the insert; and 2 inserts with a larger radius permit working with higher cutting feeds. However, the nose radius is limited not only by the tool layout but also. The nose radius, RE, is a key factor in turning operations. Inserts are available in several sizes of nose radius. The selection depends on depth of cut and feed, and influences the surface finish, chip breaking and insert strength. Depth of cut and cutting forces The relationship between nose radius and depth of cut affects vibration tendencies.
Schematic illustration of tool nose radius compensation | Download.
..
Lathe Tool Nose Radius Compensation - MachMotion.
Download scientific diagram | Schematic illustration of tool nose radius compensation from publication: Slow tool servo diamond turning of optical freeform surface for astigmatic contact lens. Tool Nose Radius Compensation Manual A look at what is required to get a radius correct 3,128 views Nov 2, 2019 Manual TNR shown graphically for external and internal radii and a.
Surface Finish Cross Reference Chart - Octane Workholding LLC.
May 24, 2022 Tool Nose Radius Compensation. When setting up the tool offsets so that the tool will machine accurately on diameter and length the tool is set to the tangent of the radius of the tool tip in the X and Z axes. When machining a taper or a radius the profile will not be accurate unless tool nose radius compensation is activated. see diagrams below. Tool Nose Radius Compensation Chart Download For Mac Note: The Haas lathe use X dimensions based on the part diameter, not the radius. Thus an X move from 0. To 1.0 X1.0 will only move the tool up.5 on the X. May 03, 2015 Learn how the CNC lathe will run your tool path using any size TOOL NOSE RADIUS with the G41 and G42 command.
Tool Nose Radius Offset | AS PRECISION.
Then you must allow for the tool nose radius compensation. Finally, to achieve a quality angle or chamfer with no burrs, we must add a G02/G03 corner break move at the start and end of the feature.... especially when using stainless steel, to eliminate burrs. The tool has a 0.0156 nose radius. N1 55DEG DIAMOND OD G97 S1000 M03 G00 X1.750.
Introduction to Turning Tools and Their Application.
Answer 1 of 4: Cutter compensation comp is used to compensate for the fact that a cutting tool has a tip radius, but you program an imaginary sharp point. Its not good practice to not use comp, because youre locking yourself into using that tool radius.
Nose Radius - an overview | ScienceDirect Topics.
. Following procedure and the chart above. Locate the required surface finish rms or AA on the vertical axis. Follow the horizontal line corresponding to the desired theoretical finish to where it intersects the diagonal line corresponding to the intended feed rate. Project a line downward to the nose radius scale and read the required nose radius. Feb 27, 2013 The numbers are for the tool orientation relative to 0 degrees. You only need to remember 2 and 3 then you can work out the others easily. On a normal lathe turning towards the chuck use 2 for boring bars and G41 Tool Nose Compensation Left and 3 for turning tools and G42 Tool Nose Compensation Right.
Solved: Compensation - Autodesk Community.
N200 G01 G42 X1.2 Z0.1 - Enable Right Hand TNC Tool Nose Compensation to account for tool nose radius when performing combined XZ motions p.130 in SL-10 Operator#x27;s Manual. N220 G01 X1.25 K-0.030 - Cut a.030quot; x 45 chamfer on corner of part using G01 corner chamfering option pp.119-121 in SL-10 Operator#x27;s Manual. N300 G00 G40 X2.1 - Cancel TNC Tool Nose Compensation at end..
How to Calculate CNC Lathe Tool Nose Radius Compensation the... - YouTube.
Register now to participate in the forums, access the download area, buy Mastercam training materials, post processors and more.... quot;Set the tool nose radius compensation value which is used for tool nose radius in Y-Z plane or the X-Y plane in advance at CUTTER R. COMP on the YI-AXIS TOOL DATA screenquot;. Quote; Link to comment. Oct 14, 2019 Case two: Using same point in software and selecting quot;In controlquot; compensation, you specify tool as having no radius, sharp point, you can do that in Fusion by selecting quot;customquot; and entering zero as radius value. Computer produces tool path following exact profile of part and outputs G41, G42 and G40 where required. About Tool Nose Radius Compensation. Calculate the Lathe Tool Nose Radius compensation to accurately machine angles. Quickly and easily calculate the CNC Lathe Tool Nose Radius Compensation needed to accurately turn angles on the OD and ID of lathe parts. No need for G41 or G42 commands with this app!.
See also: